Whirlpool 2015 Cabrio top-load washer error codes
These error code explanations can help you diagnose a problem with your Whirlpool top-load Cabrio VMAX washer. For DIY repair how-to help, visit the PartsDirect repair help section, which includes repair help for washing machines, other major appliances, lawn and garden equipment, garage door openers, vacuum cleaners and more. Search for your model number to find a complete list of replacement parts for your washer.
Long fill
Make sure that both water supply valves behind the washer are fully open. In winter, check the fill lines for freezing. Check the drain system for a siphon problem. If the water valve assembly is defective, replace it.
Excessive suds
If you see excessive suds in the washer, start using the right amount of high-efficiency (HE) detergent.
Overload
The size of the load exceeds the washer's capacity. Open the lid and remove some garments. Restart the cycle.
Spin limited by water, temperature,
This code displays when the water temperature is too high during the final spin. Spin speed is limited to 500 rpm when this code appears. Check the water valve functions using the diagnostic test mode. Replace the water valve assembly if the hot water valve sticks open.
Unbalanced load
Distribute items evenly when loading. Level the washer cabinet. Check for weak suspension springs. With the washer empty, open the lid and push down firmly on the basket. The basket should not bounce up and down more than once when pushed. Replace the suspension springs if defective.
Main electronic control board failure
Try to reset the control board by unplugging the washer for 5 minutes and then restoring power. If the F1E1 code returns after restoring power, replace the main electronic control board.
Main electronic control board failure
This code signals a failure in the motor control circuit of the main electronic control board. Unplug the washer and check the main electronic control board wiring. Check the drive motor wiring. Reconnect any loose wires. Open the lid and spin the impeller inside the basket. The impeller should rotate freely. Remove the restriction in the drive system if the impeller doesn't spin freely. If the basket spins freely, replace the main electronic control board.
Mismatch of the main electronic control board and the user interface control
The code appears when you install the wrong user interface control. Order and install the correct user interface control for your model of washer.
Stuck button
Attempt to release the stuck button. If you cannot release the stuck button, replace the user interface control.
User interface control or main electronic control board mismatched
The code appears when you install the wrong user interface control or main electronic control board. Order and install the correct user interface control or main electronic control board for your model of washer.
User interface control error
Unplug the washer. Open the console and check the wire harness connection between the main electronic control board and the user interface control. If the wire harness connection is okay, replace the user interface control.
User interface failure
Unplug the washer and replace the user interface control.
Water level signal out of range
Check the water level pressure tube for kinks, blockages or air leaks. Replace the water level pressure tube if damaged. The water level detector is a component of the main electronic control board. If the water level pressure tube is okay, replace the main electronic control board.
Water temperature sensor failure
The water temperature sensor is a component on the water valve assembly. Unplug the washer and check the wire harness connection between the main electronic control board and the water valve assembly. Reconnect any loose wires. Replace the wire harness if damaged. If the wiring is okay, replace the water valve assembly.
Lid switch error
This code displays when the lid switch detects an open lid with the lid locked. Unplug the washer and check the wire harness connections on the lid lock/switch. If the wiring connections are okay, replace the lid lock/switch.
Lid won't lock
Check for debris in the lid lock mechanism that could prevent it from locking. Unplug the washer and check the wire harness connections for the lid lock/switch on the main electronic control board. Examine the lid lock/switch assembly. If it's damaged or defective, replace it.
Lid won't unlock
Unplug the washer. Check the wire harness connections for the lid lock/switch assembly on the main electronic control board. If the connections are okay, then you will typically need to force the lid open. This will usually break the lid lock/switch. Replace the lid lock/switch if it's damaged or broken.
Lid not opened, between loads,
The main electronic control board doesn't detect the lid opening between loads. Unplug the washer and check the wiring connections between the lid lock/switch and the main electronic control board. If the wiring connections are okay, replace the lid lock/switch.
Communication error
This code signals a communication failure between the user interface control and the main electronic control board. Unplug the washer and check the wire harness between the user interface control and the main electronic control board. Reconnect any loose wires. Replace the wire harness if damaged. Replace the user interface control. If the problem persists, replace the main electronic control board.
Loss of electrical power
Plug in the power cord securely. Replace the power cord if damaged. Unplug the washer and check the power cord wiring connections on the main electronic control board. Reconnect any loose wires. Have an electrician check voltage at the electrical outlet.
Loss of power during, spin mode,
This fault code displays when power is lost during the spin mode. The washer pauses for 5 minutes to allow the spin basket to stop before continuing the cycle. Plug in the power cord securely. Replace the power cord if damaged. Unplug the washer and check the power cord wiring connections on the main electronic control board. Reconnect any loose wires. Have an electrician check voltage at the electrical outlet.
Drive motor failure
Unplug the washer and check the wire harness connections between the drive motor and the main electronic control board. Reconnect any loose wires. Replace the wire harness if damaged. Open the lid and spin the impeller inside the basket. The impeller should rotate freely. Remove the restriction in the drive system if the impeller doesn't spin freely. If the basket spins freely, replace the drive motor. If the problem persists, replace the main electronic control board.
The clutch engaged the spin basket during the wash cycle
The clutch should only engage the spin basket during the spin cycle. Unplug the washer and check the clutch for obstructions. Remove any obstructions and replace the clutch if damaged.
Clutch failure
The clutch failed to engage the spin basket in the spin mode. Unplug the washer and check the clutch for obstructions. Remove any obstructions. Replace the clutch if damaged. Check the wiring connections between the clutch and the main electronic control board. Reconnect any loose wires. Replace the wire harness if damaged. If the wiring connections are okay, replace the clutch.
Drive motor circuit failure
Unplug the washer and check the wire harness connections between the drive motor and the main electronic control board. Reconnect any loose wires. Replace the wire harness if damaged. If the wire harness is okay, replace the drive motor.
Motor not able to reach target rpm
Mechanical friction in the drive system caused by items stuck between the spin basket and tub prevents the motor from reaching the target rpm. Remove any obstructions between the spin basket and tub. An unbalanced load can also cause the F7E7 error code. Distribute items evenly when loading. Level the washer cabinet. Check for weak suspension springs. With the washer empty, open the lid and push down firmly on the basket. The basket should not bounce up and down more than once when pushed. Replace the suspension springs if defective. Unplug the washer and check the wire harness connections between the drive motor and the main electronic control board. Reconnect any loose wires. Replace the wire harness if damaged. If the wire harness is okay, replace the drive motor.
Overheated motor
Mechanical friction in the drive system caused by items stuck between the spin basket and tub can overheat the motor. Remove any obstructions between the spin basket and tub. The water level and load size detection systems may need calibrating if water level is too low for the selected cycle. Run the Service Calibration in the Service Test Mode to calibrate water level to washer cycles. A defective drive motor will overheat. Replace the drive motor if defective.
Locked rotor
The motor doesn't move when activated. Check for mechanical friction in the drive system caused by items stuck between the spin basket and tub. Remove any obstructions between the basket and tub. If there are no obstructions, replace the drive motor.
Overflow or flood condition
The electronic control senses a water level that exceeds washer capacity. Check the water level pressure tube for kinks, blockages or air leaks. Replace the water level pressure tube if damaged. Check to see if water siphons out through the drain hose. Install the washer drain system according to installation manual guidelines to prevent siphoning of fill water. A leaking water valve can cause the F8E3 code. Unplug the washer and see if the tub fills with water. If so, replace the water valve assembly.
Water hazard
This fault code displays when the main electronic control board senses water in the tub with the lid open for more than 10 minutes. A leaking water inlet valve fills the tub when the washer is off. Replace the water inlet valve if leaking.
Long drain time
This code is displayed when the water level does not change after the drain pump runs. If the washer does not drain, check the drain hose and washer drain for a clog or restriction. Unplug the washer and check the drain pump for a clog. If the drain pump is defective, replace it. If the washer is draining correctly and the drop in water level isn't being detected, replace the main electronic control board.
Most common symptoms to help you fix your washers
Choose a symptom to see related washer repairs.
Main causes: broken lid switch or lid lock, bad pressure switch, broken shifter assembly, faulty control system…
Main causes: lack of electrical power, wiring failure, bad power cord, electronic control board failure, bad user interf…
Main causes: leaky water inlet valve, faulty water-level pressure switch, bad electronic control board…
Main causes: water heater failure, bad water temperature switch, faulty control board, bad water valve, faulty water tem…
Main causes: no water supply, bad water valves, water-level pressure switch failure, control system failure, bad door lo…
Main causes: worn agitator dogs, bad clutch, broken motor coupler, shifter assembly failure, broken door lock, suspensio…
Main causes: unbalanced load, loose spanner nut, worn drive block, broken shock absorber or suspension spring, debris in…
Main causes: clogged drain hose, house drain clogged, bad drain pump, water-level pressure switch failure, bad control b…
Main causes: bad lid switch or door lock, bad timer or electronic control board, wiring failure, bad water inlet valve a…
Most common repair guides to help fix your washers
Effective articles & videos to help repair your washers
Use the advice and tips in these articles and videos to get the most out of your washer.
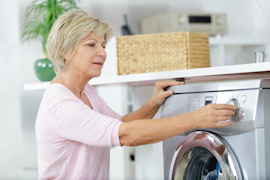
Find tips for using your washing machine efficiently to save energy and help reduce utility bills.…
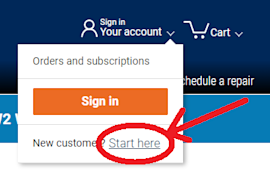
Learn about all the convenient features on our Sears PartsDirect website that make your parts purchases easier.…
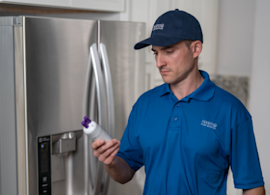
Get answers to frequently asked questions about Sears and Sears PartsDirect.…