Laundry Center: Why does my laundry'center dryer leaves clothes damp?
A blocked exhaust vent, clogged lint screen, bad timer, moisture-sensing problems, weak gas valve coils or weak heating element can prevent the load from drying fully.
To insure proper airflow through the dryer so the clothes get dry, make sure that you clean the lint screen before starting each dryer load. Hard-to-see residue from dryer fabric softener sheets also can build up on the lint screen and block airflow through the dryer, preventing clothes from drying. If you use fabric softener sheets in your dryer, remove the lint filter and scrub both sides of the screen every 6 months or so using a nylon brush and warm water to thoroughly remove residue. Rinse the filter in hot water and dry completely with a clean towel before reinstalling in the dryer. Cleaning the lint screen may restore airflow through the dryer so the clothes dry during the cycle.
Problems with the dryer timer or moisture-sensing system can prevent the clothes from getting dry in the automatic cycle. Automatic cycles in laundry center dryers vary.
Some automatic cycles use a moisture-sensing system to advance the timer and turn off the dryer when clothes are dry. The moisture-sensing system includes metal sensor bars inside the drum that detect moisture in clothes. An electronic control board detects signals from the moisture-sensing bars and advances the timer to end the automatic drying cycle when the sensor bars no longer detect garment moisture. Deposits on the bars can prevent them from detecting moisture, advancing the timer quickly and ending the automatic drying cycle but leaving clothes damp. Remove deposits you find on moisture-sensing bars using rubbing alcohol. If the sensor bars are clean, then a wiring failure or a bad moisture-sensing control board could be causing the timer to advance too quickly. Unplug the laundry center and check the wiring in the moisture-sensing system. Reconnect any loose wires and replace any broken wires. If the wires are okay, you may need to replace the moisture-sensor system's electronic control board.
Other automatic drying cycles only run the timer motor to advance the dryer timer when the heater cycles off because air temperature inside the drum trips the operating thermostat. The timer motor runs and advances the timer dial until the operating thermostat turns the heat back on because drum air temperature fell to the operating thermostat's lower temperature limit. A faulty contact in the timer can cause the timer to advance constantly instead of only when the heater cycles off. If the timer advances constantly during the automatic cycle, clothes will remain damp at the end of the cycle. Test the dryer by drying a load using a timed cycle. If the load dries using the timed cycle but stays damp when using the automatic cycle, you'll likely need to replace the timer.
If your dryer doesn't dry clothes well using a timed cycle, then a heating failure could be preventing the clothes from drying. In a laundry center that uses an electric dryer, a broken heating element can partially heat the air in the drum but not hot enough to dry the clothes. If the element breaks, the element coil can short to metal in the element housing and heat enough to warm the clothes inside the dryer but not get hot enough to fully dry the clothes. If the dryer doesn't heat up properly during the cycle, unplug the laundry center and check resistance through the heating element using a multimeter. Replace the element if you don't measure continuity through the heating element spades.
If your laundry center has a gas dryer, weak gas valve coils can prevent clothes from getting dry. Weak gas valve coils may be strong enough to open the gas valve and heat the dryer at the beginning of the cycle, but the valve coils may be too weak to open the gas valve after the first ignition. You'll likely need to replace the gas valve coils if you find the dryer heats initially but then stops heating for the remainder of the cycle.
THESE REPAIRS MAY HELP SOLVE YOUR LAUNDRY CENTER PROBLEM

Replace the laundry center dryer timer
The timer controls the components in the dryer. Also called a cycle selector, the timer has a motor that advances the internal cams inside the timer body. The cams open and close electrical contacts to energize and de-energize components during the wash cycle. A control knob on the stem of the timer lets the user select cycles on the timer. If the timer motor doesn-t advance or the contacts are defective in the timer, replace the dryer timer.
Laundry center dryer timer
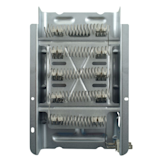
Replace the laundry center dryer heating element
The dryer heating element generates the heat needed to dry clothes. If the dryer isn't heating, check the element for visible damage and replace the heating element if it's broken. Almost all electric heating elements require 240 volts to function correctly; if the heating element won't heat even though it's getting the 240-volt power, replace it even if it doesn't look broken.
Laundry center dryer heating element
Most common symptoms to help you fix your laundry centers
Choose a symptom to see related laundry center repairs.
Main causes: clogged drain system, blocked drain hose, bad drain pump...
Main causes: broken dryer drive belt, weak drive motor, binding drum seals...
Main causes: door not fully shut, bad door switch, faulty push-to-start switch, wiring failure, bad drive motor, blown f...
Main causes: bad lid switch or lid lock, drive motor failure, broken motor coupler, bad timer, faulty electronic control...
Main causes: broken lid switch or lid lock, faulty drive motor, drain system problem, broken drive system components...
Main causes: blocked exhaust vent, clogged lint screen, bad timer, moisture sensing problems, weak gas valve coils, bad ...
Main causes: unbalanced load, broken suspension springs or shocks, worn snubber ring...
Main causes: lack of water supply, failed lid switch or lid lock, bad water level pressure switch, control system failur...
Main causes: control system failure, broken heating element, bad gas valve coils, gas supply failure, voltage supply pro...
Most common repair guides to help fix your laundry centers
These step-by-step repair guides will help you safely fix what’s broken on your laundry center.
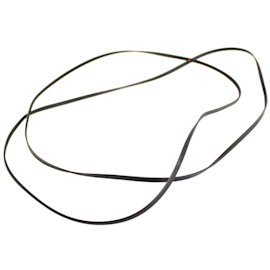
How to replace a laundry center dryer drive belt
If the dryer motor runs but the drum doesn’t turn, the drive belt is likely broken. Replace it, following the steps in t...
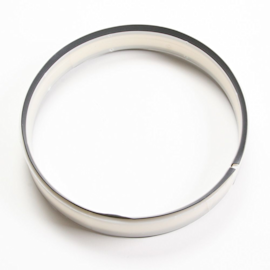
How to replace a laundry center washer snubber ring
If the washer tub bangs the cabinet during the spin cycle even though the load is balanced, you might need to replace th...
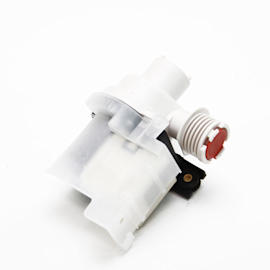
How to replace a laundry center washer drain pump
If the washer won’t drain because the drain pump failed, follow the steps in this repair guide to replace it....
Effective articles & videos to help repair your laundry centers
Use the advice and tips in these articles and videos to get the most out of your laundry center.
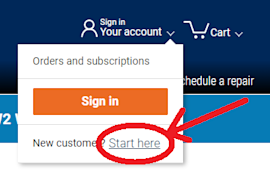
Learn about all the convenient features on our Sears PartsDirect website that make your parts purchases easier....
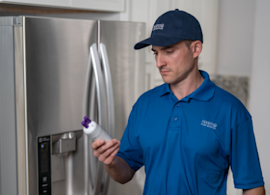
Get answers to frequently asked questions about Sears and Sears PartsDirect....
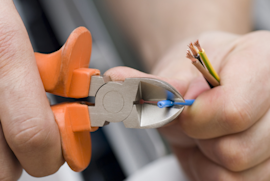
Learn how to repair broken, frayed or damaged wires in your appliances....